Today’s warehouses play a vital role in the overall efficiency of factories and the supply chain. Technology advancements have enabled warehouses to operate more efficiently and effectively, from automating tasks to improving the accuracy of inventory management, technology has had a profound impact on warehouse operations.
It’s also important to point out that the same macro headwinds affecting research, engineering, and the factories also impact the warehouse. Workforce shortages, high turnover, and a lack of skilled warehouse associates are fueling investments that manufacturers might have otherwise ignored in years past. The cost of not automating, not augmenting the workforce, and not scaling up productivity is greater than the cost of warehouse technology investment.
Popular Investments
Where are manufacturers investing in warehouse operations? The following are some of the most common investments we’re seeing and supporting with our clients:
1. Automated Material Handling Systems (AMHS)—Automated Material Handling Systems use robots, conveyors, and automated storage and retrieval systems to handle materials in a warehouse efficiently. This technology has dramatically improved inventory management’s speed and accuracy, and reduced the need for manual labor.
2. Warehouse Management Systems (WMS)—Warehouse Management Systems are software solutions that help manage and optimize warehouse storage, retrieval, and inventory distribution. This technology provides real-time data on inventory levels, order status, and shipping schedules, enabling warehouse managers to make informed decisions. WMS software also runs atop of the modern hardware devices used by the put and pick, receiving, and shipping processes to improve how work gets done correctly every time. These platforms also integrate with ERP, 3PL, and transportation and logistics companies to drive a more efficient supply chain.
3. Radio Frequency Identification (RFID)—Radio Frequency Identification is a wireless technology used to track the movement of inventory in a warehouse. RFID tags are attached to products, and RFID readers are used to track their movement in real time. This technology has greatly improved inventory management accuracy and reduced the time required to locate products in a warehouse. The technology can also streamline and automate many transactions, allowing warehouse associates to focus on more value-added activities.
4. Warehouse Robotics—Warehouse robotics includes a range of technologies, including pick-and-place robots, mobile robots, autonomous guided vehicles (AGVs), and autonomous mobile robots (AMRs). These technologies automate tasks such as order picking, packing, and transporting goods, freeing up human workers to focus on more complex tasks. Warehouse robotics has greatly increased warehouses’ efficiency and productivity and reduced the risk of injury to workers.
5. Network Infrastructure—I would be remiss by ignoring the underlying infrastructure. We hear it all the time from our manufacturing clients. They implement new technologies, whether that is mobile scanners, forklift mobility, tablets, or AMRs at scale, but fail to include robust wireless, directional antennas, or modern technologies like private cellular.
Traditional networking done right ensures all endpoints have a strong signal and no dead spots, which are critical to ensure positive end-user adoption and productivity. Private cellular is another great technology. It allows your organization to deliver strong 5G signals anywhere in the warehouse, eliminates access point hopping, and provides constant access for high mobility and high bandwidth applications. Most warehouse devices natively support 5G, and when it comes to the high mobility use cases, including forklifts and AMRs.
Forklifts Deserve Love Too
In manufacturing, we often speak to the most advanced technologies surrounding smart manufacturing or Industry 4.0, like artificial intelligence and robotics. Not every business is ready to adopt the latest technologies in the marketplace. Investing in forklift software, mounted tablets, and modern warehouse scanners can significantly increase productivity and support growth.
Like any other business process, opportunities to simplify and increase forklift productivity will help mitigate workforce challenges or help your business scale to match growth in demand. Whether your business is performing paper-based picking, or looking to upgrade that old end-of-life forklift technology, modern forklift solutions have advanced and can provide more capabilities to improve productivity and ergonomics, support a wide range of tasks, and even contribute to improved safety.
For example, some solutions detect possible collisions, prevent mobile device usage while in motion, and even reduce fatigue or repetitive injury through product design.
Let’s Make It Happen
We understand that manufacturers are at different points in their smart warehouse operations. Our Manufacturing Practice regularly works with manufacturing organizations to help them grow and improve their business by applying enabling technologies to maximize warehouse resources, and support business objectives.
Our Manufacturing Practice has a team of experts from trade and an evolving portfolio of manufacturing solutions. It assists IT and OT teams by augmenting their existing skillsets with complimentary advisory services to help your business accelerate technology adoption where it matters most. If your business is interested in learning more about how we support modern warehouse operations, engage Connection’s Manufacturing Practice to discover more about this technology, available services, and the many use cases that may benefit your organization.
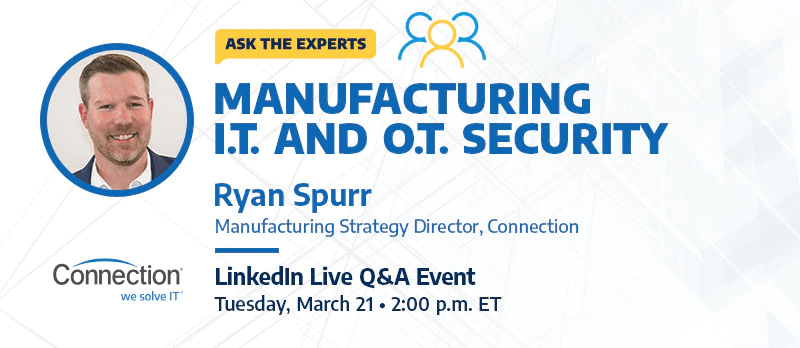
Don’t miss our upcoming LinkedIn Live event covering a number of security topics related to the manufacturing industry. Submit your questions now!