So many manufacturing conversations regarding business continuity and disaster recovery (BCDR) go like this when it comes to the plant floor: “We have an employee who walks around and periodically backs up our machines.” “We can live without some amount of data for a couple of days.” Or the classic, “We can make up lost production time with shifts through the weekend.” It’s frustrating to watch the most business-critical process in a manufacturing company be so undervalued that we don’t apply the same rigors we find in data centers to the profit-generating infrastructure building our customers’ products.
This approach is an outdated mindset, and the assertions are falsely based on inaccurate risk assessments that wildly underestimate the actual impacts. In my experience, this only works if your goal is to check a box vs. a fundamental strategy of remaining online and operational all the time. Why are manufacturers so hyper-focused on uptime and overall equipment effectiveness (OEE) but not on quickly recovering critical machines or an entire facility?
For example, past BCDR strategies worked fine when the only threat to your factory was a computer, disk, or software failure. But today’s plants are packed with a mix of legacy and modern technologies that the business depends upon to produce products uninterrupted. The recent pandemic also taught us that resiliency isn’t just about backups, but how quickly we can recover our facilities’ operations in an automated and unattended fashion. That employee running around with a USB stick may not be available when you need them most, or the backups stopped when that employee took a job promotion at a competitor.
Layer in the mounting cybersecurity events targeting the plant floor, and we are seeing a rapid increase in the frequency, impact, and outage periods. In 2020, manufacturing became the second most targeted industry with an alarming 33% of all cyber-theft incidents occurring in manufacturing. It’s now common for manufacturing plants to shutter for days or weeks as they recover lost data, rebuild machines, and return a plant to operation. Investment into security technology and resources is finite. Recent events are demonstrating that 31% of manufacturing experience unplanned failures in the plant and data centers, often resulting in significant downtime.
Another reality we must consider is the continued rise in technology adoption amongst U.S. manufacturers to combat global pressures and any prevailing market headwinds. Whatever your company’s level of technology adoption to date—you should only expect more technology to be added into existing processes—not less.
Manufacturers should all be asking themselves the following questions. How will your organization quickly recover corporate business systems and critical factory technology? How will your business minimize brand, sales, and customer impacts? How will your organization quickly restore your entire operational landscape in a mass security event? Would your organization be able to restore to anywhere, anytime, and with any resource?
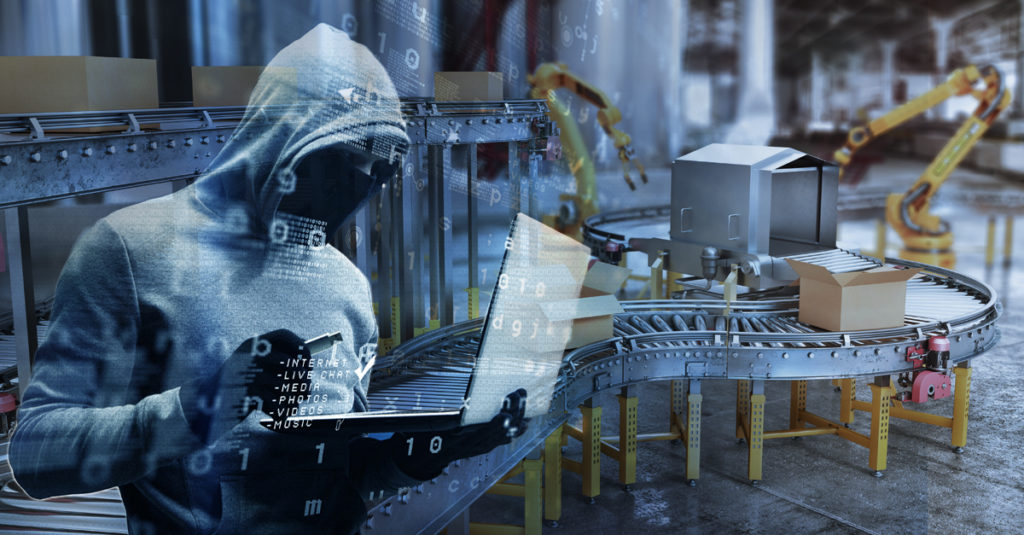
The good news is there are many options available to protect your tech estate. Modern solutions exist that appeal to both traditional data center needs as well as the more heterogenous and legacy-based environment we see in factories, warehouses, and research. These solutions provide support for a wide range of operating systems and devices, and they integrate across the OT/IT landscape. Solutions can also span your hybrid environments, protecting physical plant machines, virtual machines, and other services in the cloud like AWS, Azure, Google, Microsoft 365, and more. Employees depend on all these resources, not just ERP.
If your organization lacks experience or skillsets, or is looking for staff augmentation, managed service offerings can also bring expertise in devising an integrated backup and disaster recovery solution that fits your business needs. Many also provide services to aid in the ongoing operational activities around backup, monitoring, and recovery in the event a disaster does strike.
Business continuity and resiliency are becoming more essential in companies as industrial transformation (IX) and technology adoption increase. Combine the financial and productivity impacts with effects on workforce morale, distractions from value-added activities, and impact on brand and deliverables, and your modern organization should be changing its view of business continuity and resilience risks. The risks are no longer realized in the off chance a weather event bears down on your facility, it’s now a combination of catastrophes, cybersecurity, unplanned failure or human error, and workforce disruption.
To learn more about Connection’s Manufacturing Practice or to discuss the challenges and edge compute solutions highlighted in this article, contact us today.